We make a hiller for a walk-behind tractor on our own
The hilling procedure for potatoes is carried out several times per season. If we are talking about small areas, hilling is carried out without resorting to the help of agricultural equipment. As for large areas, it is difficult to handle them by hand. Let's talk how to make a hiller for a walk-behind tractor with our own hands, and consider what types of hillers exist.
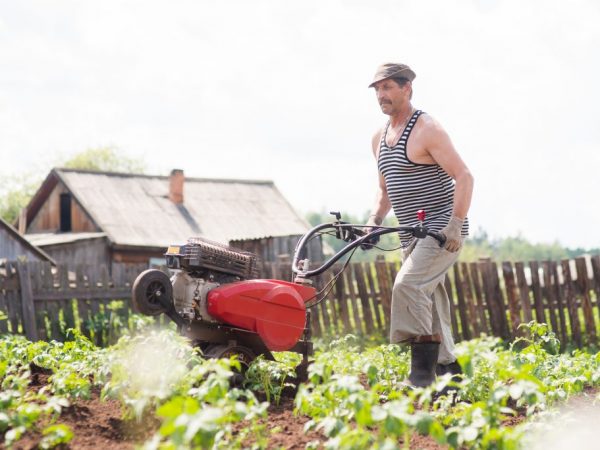
Hiller for a walk-behind tractor independently
Classification of hillers
To build convenient and functional equipment, you need to figure out what types of hillers exist. There are several classifications of this equipment. Let's consider each of them.
Type of equipment
On sale there are the following types of potato hillers for a walk-behind tractor:
- listerous;
- disk;
- propeller.
The most popular are disc and lister hillers. Their design is simple, allowing you to reproduce the equipment yourself. Other types of hillers are more difficult to manufacture. In addition, for small areas, a lister or disk model is enough.
It makes sense to think about purchasing or making more complex structures when it comes to the industrial cultivation of potatoes.
Advantages of hillers of each type
The Lister model is lightweight, which allows it to be attached to low-power equipment. It does not overload the walk-behind tractor, even when working with heavy soils.
With the help of disk models, which are well combined with the design of the walk-behind tractor, the work can be performed more efficiently. Another advantage is that during operation, you can adjust the width of the land. In addition, the disc structure can be used as a weeder.
It is advisable to attach propeller-type structures only to those motor cultivators equipped with several frontal Gears. Working with such equipment, in addition to loosening the soil, it will be possible to transfer it from the row spacing to the furrows. Propeller-type structures are difficult to make on your own.
On the market there are single-row and n-row models of each type (double, triple, etc.). Multi-row designs are designed to process several rows at the same time.
Hiller functionality
There are 2 types of equipment:
- passive;
- active.
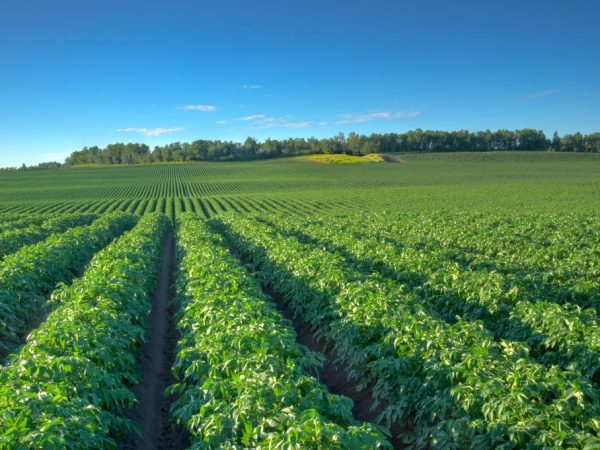
Nicely spud potatoes
Passive equipment is used exclusively for hilling vegetable crops. As for the active hillers for the walk-behind tractor, with their help they carry out almost all types of land work (planting, hilling, loosening, harvesting). This technique is equipped with a rotor. Accordingly, it works in an automated manner. It is difficult to build it at home without having certain skills. If there is a need for such a hiller, it is better to buy it.
Design features
There are regulated and unregulated hillers.When working with an adjustable hiller for a walk-behind tractor, you can adjust the depth of cultivation, as well as the width of the cultivated area.
With adjustable equipment, you can handle crops with varying row spacings, but they tend to be heavy. It is not recommended to attach them to low power cultivators. In addition, when working with adjustable structures, part of the soil crumbles back when making furrows.
Before installing the attachment, read the instructions for the cultivator, which indicates how appropriate it is to do so.
DIY lister hiller
This is the simplest type of device, which does not take a lot of time and money to manufacture. Before making a product, it is advisable to make a drawing of a lister hiller for a walk-behind tractor, observing the proportions between all structural elements. The drawing will show all the shortcomings and oversights, which at the manufacturing stage will be more difficult to correct than at the stage of thinking over the course of work.
In general, the product looks like a miniature version of a plow.
Necessary materials
To make a do-it-yourself hiller for a lister-type walk-behind tractor, you will need:
- a square metal pipe (2x2 or 3x3) or a metal rod, the width of which is 3 cm and the depth is 1.5 cm;
- metal sheet, the thickness of which is 2 mm or more;
- strips made of metal with a thickness of 3 mm and 4 loops when it comes to an adjustable hiller.
The dimensions of the sheet metal depend on the dimensions of the finished product. In addition to materials, you will need a welding tool and a grinder, electrodes, a hammer and keys.
Execution of works
- Using a previously prepared template made of metal with a thickness of 2 mm, we cut out the side parts of the product, which, due to some similarity, are called ears. The width and shape of the ears can be arbitrary. The wider the ears, the more soil is poured under the potato bush. When making a product, the method of planting potatoes is taken into account. If the aisles are narrow, the ears should be narrow. If the aisles are wide, you can make wider ears (10-15 cm). The average length of the ears should be 25 cm. In the narrowest part, the width of the ears is 5-7 cm.
- At this stage, the shape of the side parts of the homemade hiller is formed. It should be curved. In this case, the bending radius of both ears should be the same. The adjustment should be done as accurately as possible. Then the ears are welded and the seams are processed with a grinder to get an absolutely even top layer of metal.
- With the help of strips, they connect the ears to each other. Each of the strips is welded or attached to the ears with loops. Then the strips are welded together. Most often, the design is made so that the strips are located in relation to each other at an angle of 90 °, and the side parts are 120 °.
- In order for the equipment to enter the ground without problems, it must have a sharp end, which is called a spout. It is welded to the rest of the structure so that the angle between the strips holding the ears and the nose is 150 °. Ultimately, you should get a solid structure, without any gaps or protrusions. We weld the spout to the main part of the structure and additionally fasten it with a metal plate.
- At the final stage of work, we weld a bracket to the main part of the structure, with which the hiller is attached to the cultivator. Alternatively, you can weld two metal strips to the inside by making holes at the other end of the size corresponding to a large bolt. We make the same holes in the bracket. Using a bolt and a nut, we attach the bracket to these strips. You can weld the strips to the bracket for a more secure fit.
- We sharpen the ends of the product so that they easily enter the ground.
This is a general scheme that allows you to make a hiller on a walk-behind tractor with your own hands.You can make adjustments to it based on your own preferences and the available tool. Alternatively, you can make a two-row hiller by connecting 2 structures made according to the above scheme with a beam. It is advisable to make the main part of the structure removable so that it is fashionable to change the width between the blades of the hiller. If the main part is welded to the beam, then, when planting potatoes, we make the row spacing corresponding to the distance between the blades of the hiller.
The only part worth buying is the hitch. The cultivator hitch is sold in specialized stores. There are different sizes of parts and design options. It is not difficult to install it. And it will increase the reliability of fastening several times.
Do-it-yourself disk hiller
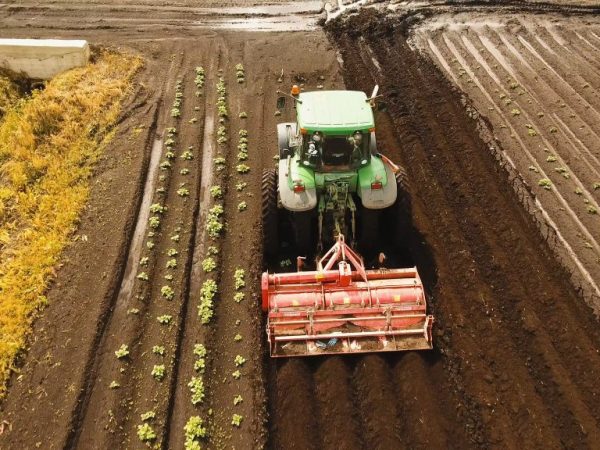
Okunchiks are attached to walk-behind tractors and tractors
More versatile is the disc type of the hiller for the walk-behind tractor.
Necessary materials
We need:
- sheet steel, at least 3 mm thick;
- rack;
- mounting bolts and washers;
- bearings with oil seals;
- metal pipe.
The equipment you need is the same as in the manufacture of the previous model. Before creating the equipment, we make a drawing.
Execution of works
- In order not to make discs from sheet steel, we use cutters from a collective farm seeder, which can be purchased at markets where various used equipment is sold. If you could not find the cutters, we cut out circles of the corresponding diameter from sheet steel (for potatoes 40-45 cm). Alternatively, we use pot lids, pre-sharpened around the edges. But, this is not the best option.
- We bend the metal discs so that they are slightly convex on one side, and on the other, respectively, slightly concave. It is easier to work with such equipment. After bending, the distance between the edges of the discs on the ground should be the same. It is very important to get symmetrical disk hardware. If inaccuracies are allowed at this stage, then the subsequent adjustment will not give the desired result.
- We attach the discs to metal struts made of sheet steel. We use fastening bolts and washers. We install bearings. You can do without bearings, but later on it will be inconvenient to work with the tool.
- We attach both racks to a metal pipe. The distance between the discs must correspond to the distance between the rows. Place the discs at a slight angle (15-20 degrees) in relation to each other. It is advisable to make stands with disks removable so that the tool can be used for hilling different vegetable crops that sit at different distances from each other.
- We weld a metal plate or a pipe of a smaller diameter to the horizontal pipe, which will be attached to the bracket of the cultivator with the help of fastening bolts. Since the load on the equipment when working with heavy soils is high, make sure that the coupling of the homemade hiller and the walk-behind tractor is reliable.
The equipment is ready for use. As in the previous version, this is a rough diagram describing the main stages of work. A horseshoe-shaped welded metal piece can be used to connect the discs. It is easier to build such a structure, but it is less functional. Since it is impossible to change the width between the discs of the finished product.
It is better to place the hiller in front of the walk-behind tractor. The same applies to attachments, with the help of which the rows are cut. But the harrow, for example, clings to the back.
Important points
- The attachments, it does not matter, we are talking about lister or disc hillers, with a sliding structure, it is advisable to attach only to walk-behind tractors, the mass of which exceeds 30 kg. There are requirements for the power of the walk-behind tractor. It should not be less than 4 horsepower (Oka, for example).For less powerful motoblocks, it is advisable to use a single-row hiller or two-row, but with a constant width between the discs or "plows".
- It is important to choose the right materials for the manufacture of equipment. Give preference to steel, which contains alloying components. They make the metal more durable and resistant to corrosion. Pay attention to the thickness of the sheet. Equipment, the main elements of which are made of thin steel, will be ineffective.
- Elements penetrating into the ground should be streamlined. Otherwise, when using the technique, more soil is turned inside out. And this contributes to the rapid loss of moisture. Accordingly, all crops growing in the cultivated area will have to be watered much more often.
- When purchasing a motor-cultivator, make sure that it is provided for hanging additional passive equipment. As for motoblocks, which are more powerful than cultivators, there are no such problems with them. All models can be attached to home-made or factory-made additional passive equipment.
- Do not forget to adjust the angle and immersion depth of the hinged homemade structure before use.
Conclusion
It is not difficult to make attachments for motoblocks with your own hands. Disc and propeller structures must be adjusted before use. It is important and correct to choose a walk-behind tractor. The models Cascade, MTZ, Oka, Salyut, Agromash, MB-1, Neva, Agro, Kentavr, Krot, Patriot, Ugra are popular today. Many opinions revolve around the Oka cultivator. Some complain that belts wear out quickly. Some say that the quality of the parts does not match the pricing policy. But, despite this, the Oka cultivators are in demand. In addition, the Oka is a powerful unit that works without problems on heavy soils and virgin soil.